страница - 54
2.3.7.4. ИСПЫТАНИЯ НА ТВЕРДОСТЬ ПО ВИККЕРСУ
Метод измерения твердости по Виккерсу черных и цветных металлов и сплавов при нагрузках от 9,807 Н (1 кгс) до 980,8 Н (100 кгс) основан на вдавливании алмазного наконечника в форме правильной четырехгранной пирамиды в образец (изделие) под действием нагрузки Fy приложенной в течение определенного времени, и измерении диагоналей отпечатка , d2, оставшихся на поверхности рабочего образца после снятия нагрузки (рис. 2.3.20).
Твердость по Виккерсу (HV) вычисляют по формулам:
0,102-2jF sin-
HV =-z-2. = 0,189-х-,
d2d2
где F - нагрузка, H;
. a 2 jFsin-
HV=-j-2. = 1,854,
d2d2
где F - нагрузка, кгс; a - угол между противоположными гранями пирамиды при вершине, равный 136°; d - среднее арифметическое значение длин обеих диагоналей отпечатка после снятия нагрузки, мм.
Для определения твердости по Виккерсу берут среднее арифметическое значение длин обеих диагоналей. Разность диагоналей одного отпечатка не должна превышать 2 % меньшей из них.
Для анизотропных материалов получаемая разность длин двух диагоналей одного отпечатка может не укладываться в указанный допуск. Допуск на эту разность должен быть указан в стандартах или технических условиях на металлопродукцию.
Измерение диагоналей длиной до 0,2 мм включительно должно производиться с погрешностью не более ±0,01 мм и для диагоналей длиной более 0,2 мм - с погрешностью не более ±0,5 %.
Твердость по Виккерсу при условиях испытания F = 294,2 Н (30 кгс) и времени выдержки под нагрузкой 10 - 15 с обозначается цифрами, характеризующими величину твердости и буквами HV. При других условиях испытания после букв HV укалывается нагрузка и время выдержки.
т
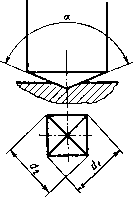
Рве. 2.3.20. Способ измерения твердоств по Виккерсу с помощью алмазной пирамиды
Примеры обозначения:
500 HV - твердость по Виккерсу, полученная при нагрузке F = 30 кгс и времени вьщержки 10 - 15 с;
220 HV 10/40 - твердость по Виккерсу, полученная при нагрузке 98,07 Н (10 кгс) и времени выдержки 40 с.
Поверхность испытуемого образца должна иметь шероховатость не более 0,16 мкм и быть свободной от окисной пленки и посторонних веществ.
При измерении твердости должна быть обеспечена перпендикулярность приложения действующего усилия к испытуемой поверхности.
При измерении твердости алмазной пирамидой применяются следующие нагрузки Н (кгс): 9,807 (1); 19,61 (2); 24,52 (2,5); 29,42 (3); 49,03 (5); 98,07 (10); 196,1 (20); 294,2 (30); 490,3 (50); 980,7 (100).
Для получения более точного результата измерения твердости нагрузка должна быть возможно больше, причем на обратной стороне образца не должно быть заметно следов деформации.
Для определения твердости черных металлов и сплавов применяют нагрузки от 49,03 Н (5 кгс) до 980,7 Н (100 кгс); для меди и ее сплавов - от 24,52 (2,5 кгс) до 490,3 Н (50 кгс);для алюминиевых сплавов - от 9,807 Н (1 кгс) до 980,7 (100 кгс).
При измерении твердости должны быть соблюдены следующие условия:
плавное возрастание нагрузки до необходимого значения;
поддержание постоянства приложенной нагрузки в течение установленного времени.
Продолжительность выдержки под нагрузкой должна составлять 10 - 15 с.
Расстояние между центром отпечатка и краем образца или краем соседнего отпечатка должно быть не менее 2,5 длины диагонали отпечатка. Минимальная толщина образца должна быть для стальных изделий больше диагонали отпечатка в 1,2 раза; для изделий из цветных металлов - в 1,5 раза.
При неизвестной толщине испытуемого слоя следует произвести несколько измерений при различных нагрузках. Если при этом твердость будет изменяться, то следует уменьшать нагрузки до тех пор, пока при двух смежных нагрузках твердость не будет близка по своим значениям или совпадать.
Испытания проводят при температуре
20
+15 -10
•С.
2.3.7.5. ИСПЫТАНИЯ НА ТВЕРДОСТЬ МЕТОДОМ УДАРНОГО ОТПЕЧАТКА
Метод основан на внедрении в поверхности испытуемого объекта твердосплавного конического индентора (для испытания стали с твердостью < HV 850) или стального шара (для испытания стали с твердостью £ НВ 350).
Измерение сравнительной твердости стали по Виккерсу, Бринеллю и пластической твердости осуществляется с помощью переносных твердомеров ударного действия при начальной скорости удара от 1 до 5 м/с.
При измерении сравнительной твердости стали по Виккерсу твердосплавный наконечник в форме двустороннего или одностороннего конуса с углами ср = 136° при вершинах внедряют в поверхности испытуемого объекта под действием кратковременной динамической нагрузки Рд, создаваемой ударным механизмом. После снятия индентора с испытуемой поверхности измеряют диаметры отпечатков конуса на поверхностях контрольного бруска d3 и испытуемого образца (объекта) d$ (рис. 2.3.21).
Число сравнительной твердости испытуемого объекта по Виккерсу (HVC) вычисляют по формуле
HV =HV.
где НУЭ - среднее значение твердости контрольного бруска по Виккерсу, измеренное посредством статического стационарного прибора; d3 и d0 - диаметры ударных отпечатков конуса на поверхностях стального контрольного бруска и испытуемого объекта, мм; гкэ и т)ко - динамические коэффициенты твердости материалов стального контрольного бруска и испытуемого объекта при ударном внедрении конуса (со скоростью внедрения 1-5 м/с).
При измерении этим методом сравнительной твердости по Бринеллю стальной шарик диаметром D одновременно внедряют в поверхности стального контрольного бруска и испытуемого объекта под действием кратковременной нагрузки Рд, создаваемой ударным
механизмом.
После снятия индентора с испытуемой поверхности измеряют диаметры отпечатков шарика на поверхностях контрольного бруска и испытуемого объекта или глубины восстановленных отпечатков на поверхностях объекта Л0 и стального контрольного бруска Лэ (рис. 2.3.22).
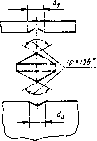
Рис. 2.3.21 Схема нзмеревжя твердости по Внккерсу с помощью двустороннего конуса
и
Ы-4
Рас. 2.3.22. Схема измерения твердости методом ударного отпечатка с помощью стального шарик*
Число сравнительной твердости испытуемого объекта по Бринеллю (НВС) вычисляют по формуле
нвс =нв:
D-JD2-dl Лшэ D-D1 -d] Лшо
где НВЭ - среднее значение твердости по Бринеллю стального контрольного бруска, измеренное посредством стационарных статических приборов ТШ или ТК; D - диаметр шарика, мм; d3 и Лэ - диаметр и глубина восстановленного ударного отпечатка на поверхности контрольного бруска, мм; d0 и h0 - диаметр и глубина восстановленного ударного отпечатка на поверхности испытуемого образца, мм;
динамические коэффициенты
твердости стального контрольного бруска и испытуемого образца (объекта) при ударном внедрении шарика со скоростью 0,72 + 2 м/с.
Диаметры отпечатков измеряют в двух взаимно перпендикулярных направлениях и определяют как среднее арифметическое результатов двух измерений. Разность измерений диаметров одного отпечатка не должна превышать 2 % меньшего из них.
Измерение диаметров ударных отпечатков конического индентора на испытуемой поверхности и поверхности контрольного бруска должно осуществляться с помощью отсчетного оптического микроскопа, погрешность которого не должна превышать ±0,01 мм на одно наименьшее деление шкалы.
Измерение диаметров ударных отпечатков шарика на испытуемой поверхности и поверхности контрольного бруска должно осуществляться с помощью отсчетного оптического микроскопа, погрешность которого не должна превышать ±0,5 мм на одно наименьшее деление шкалы.
Измерение глубины отпечатков шарика на испытуемой поверхности и поверхности контрольного бруска должно осуществляться индикаторным глубиномером с ценой деления 0,01 мм.
Применяемые при измерении сравнительной твердости по Бринеллю и пластической твердости стальные шарики должны соответствовать следующим требованиям:
материал для шариков - термически обработанная сталь с твердостью не менее HV 850;
диаметры шариков 5 и 10 мм;.
поверхность шарика не должна иметь пороков, видимых с помощью лупы при 5-кратном увеличении.
Применяемый при измерении сравнительной твердости по Виккерсу двусторонний или односторонний конус из твердого сплава должен иметь образующие углы 136±10° при вершинах и закругленные вершины с радиусом сферы не более 0,2 мм.
Поверхности конусов на протяжении 0,3 мм от вершины, считая по его оси, должны быть тщательно отполированы и свободны от трещин и других пороков, видимых с помощью лупы при 30-кратном увеличении.
Минимальная толщина испытуемого образца должна быть не менее 10-кратной глубины отпечатка.
При испытаниях приборами с шаровым индентором применяют стальные контрольные бруски сечением 10x10 мм любой твердости в интервале НВЭ 120 - 200.
При испытаниях приборами с двусторонним конусом применяются стальные контрольные бруски сечением 4,5x4,5 мм любой твердости в интервале HV 100 - 320.
2.3.7.6. ДРУГИЕ МЕТОДЫ ИСПЫТАНИЙ НА ТВЕРДОСТЬ
Метод измерения твердости металлов и сплавов по Шору. Боек определенной массы с алмазным наконечником свободно и вертикально падает с определенной высоты на испытуемую поверхность. Высота отскока бойка принимается за характеристику твердости и измеряется в условных единицах.
Масса изделия при измерении твердомерами, установленными непосредственно на изделие, должна быть не менее 5 кг. Образцы, устанавливаемые на столик твердомера, должны иметь массу не менее 0,1 кг и толщину не менее 10 мм.
Прибор для измерения твердости должен обеспечивать:
высоту отскока бойка h\ для 100 единиц твердости по Шору - 13,6 ± 0,3 мм;
высоту падения бойка hi - 19,0 ±0,5 мм; цену деления- индикатора (измерителя высоты отскока бойка) не более 1 единицы шкалы HSP.
Масса бойка t алмазным наконечником должна быть 36 г.
Твердость по Шору указывают с округлением до целой единицы. В шкале Шора за 100 единиц принята максимальная твердость стабилизированного после закалки на мартенсит образца из углеродистой инструментальной стали, что соответствует высоте падения бойка hi = 13,6 ± 0,3 мм.
Акустический метод определения твердости образца основан на измерении относительных изменений механического импеданса колебательной системы преобразователя в зависимости от механических свойств поверхности образца.
содержание:
[стр.Введение] [стр.1] [стр.2] [стр.3] [стр.4] [стр.5] [стр.6] [стр.7] [стр.8] [стр.9] [стр.10] [стр.11] [стр.12] [стр.13] [стр.14] [стр.15] [стр.16] [стр.17] [стр.18] [стр.19] [стр.20] [стр.21] [стр.22] [стр.23] [стр.24] [стр.25] [стр.26] [стр.27] [стр.28] [стр.29] [стр.30] [стр.31] [стр.32] [стр.33] [стр.34] [стр.35] [стр.36] [стр.37] [стр.38] [стр.39] [стр.40] [стр.41] [стр.42] [стр.43] [стр.44] [стр.45] [стр.46] [стр.47] [стр.48] [стр.49] [стр.50] [стр.51] [стр.52] [стр.53] [стр.54] [стр.55] [стр.56] [стр.57] [стр.58] [стр.59] [стр.60] [стр.61] [стр.62] [стр.63] [стр.64] [стр.65] [стр.66] [стр.67] [стр.68] [стр.69] [стр.70] [стр.71] [стр.72] [стр.73] [стр.74] [стр.75] [стр.76] [стр.77] [стр.78] [стр.79] [стр.80] [стр.81] [стр.82] [стр.83] [стр.84] [стр.85] [стр.86] [стр.87] [стр.88] [стр.89] [стр.90] [стр.91] [стр.92] [стр.93] [стр.94] [стр.95] [стр.96] [стр.97] [стр.98] [стр.99] [стр.100] [стр.101] [стр.102] [стр.103] [стр.104] [стр.105] [стр.106] [стр.107] [стр.108] [стр.109] [стр.110] [стр.111] [стр.112] [стр.113] [стр.114] [стр.115] [стр.116] [стр.117] [стр.118] [стр.119] [стр.120] [стр.121] [стр.122] [стр.123] [стр.124] [стр.125] [стр.126] [стр.127] [стр.128] [стр.129] [стр.130] [стр.131] [стр.132] [стр.133] [стр.134] [стр.135] [стр.136] [стр.137] [стр.138] [стр.139] [стр.140] [стр.141] [стр.142] [стр.143] [стр.144] [стр.145] [стр.146] [стр.147] [стр.148] [стр.149] [стр.150] [стр.151]